HZS120 Concrete Batching Plant
clicks:4227
Capacity: |
120 m3/h |
Mixing Time: |
60 S |
Max Aggregate Size: |
60/80mm |
Discharging Height: |
4000 mm |
Total Power: |
160KW |
Total Weight: |
100Ton |
Total Dimensions: |
42x26x19.4m |
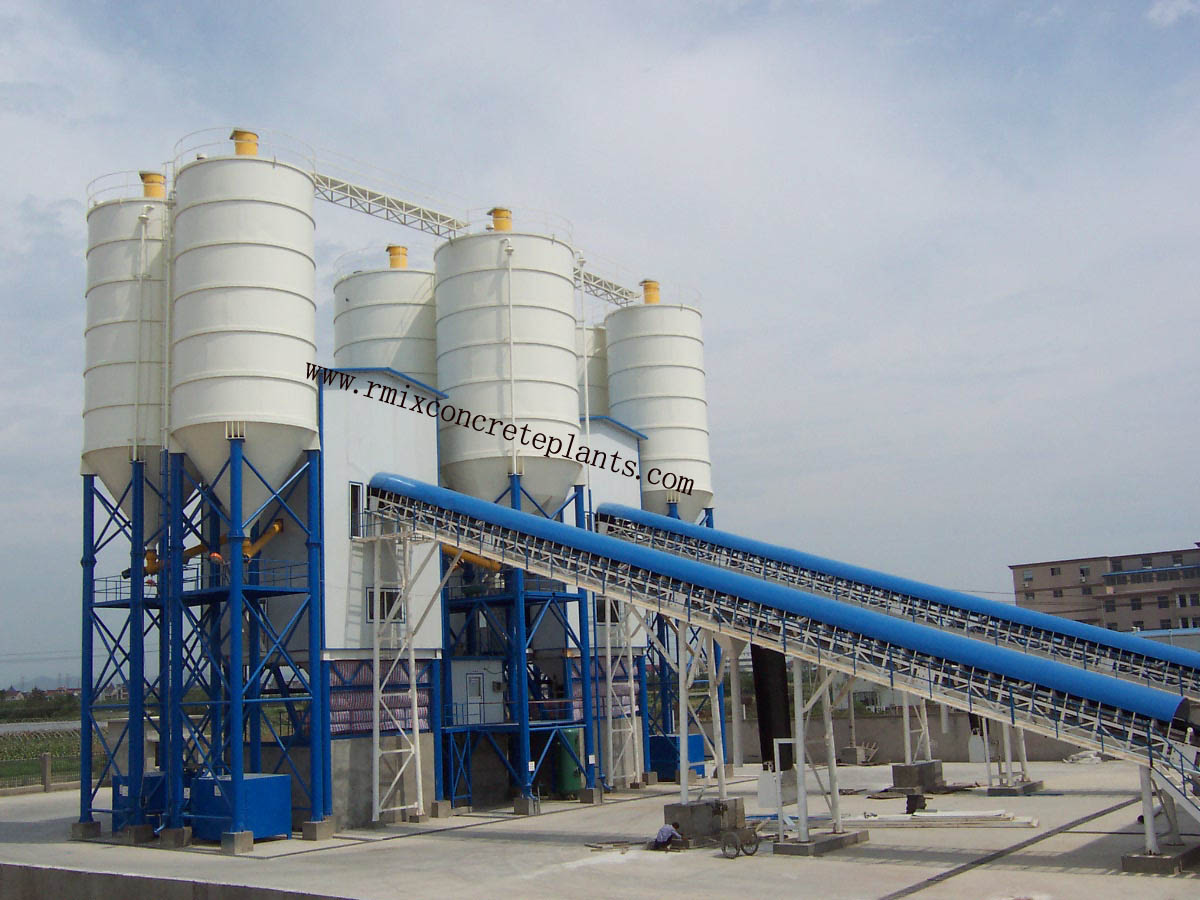
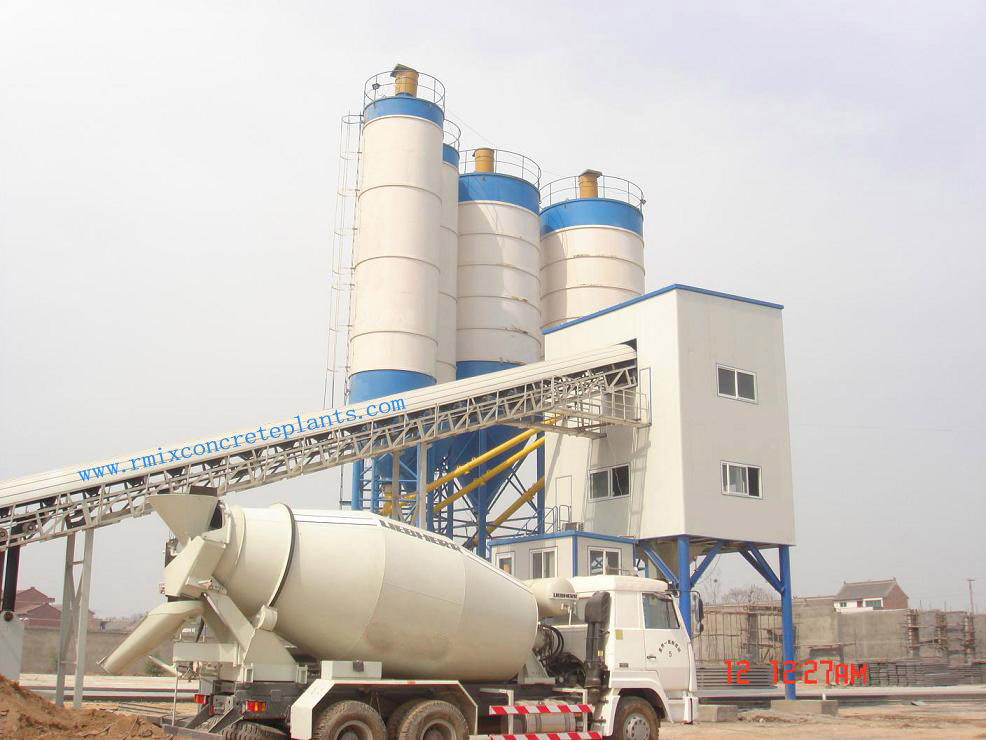
HZS120 Concrete Mixing Plant
Descriptions of Concrete Mixing Plant:
HZS120 plant is belt type central mix concrete batching plant with capacity ranging from 100–120 m3/hr. It is the perfect solution for the big ready concrete producer or construction site. This HZS modular batching plants are designed for locations where layout flexibility. It is a great central concrete batching plant for a invent business.
We focus on minimizing "soft costs"—set up, site preparation, operating costs and repairs. HZS plants feature a smaller footprint, require far less site preparation and are easier to set-up. Plumbing and wiring are already installed and factory tested. Many parts are manufactured from hot-dip galvanized steel to minimize corrosion.
Application of Concrete Mixing Plant:
This stationary concrete batching plant is widely used for water conservancy ,electric power, railroad, road, tunnel , the arch of bridge, harbor-wharf and the national defense-project etc..HZS120 is your smart choice and expand as your business grows.
Technical Parameters of HZS120 Ready Concrete Mixing Plant:
Capacity:
120 m3/h
Mixing Time:
60 S
Max Aggregate Size:
60/80mm
Discharging Height:
4000 mm
Total Power:
160KW
Total Weight:
100Ton
Total Dimensions:
42x26x19.4m
1. Mixer: Twin Shaft Concrete Mixer
Model:
JS2000-Ⅱ
Mixer Capacity:
2000L
Feeding Capacity:
3200L
Fresh Concrete Capacity:
2250L
Compacted Concrete Capacity:
2000L
Mixing blade:
2×8PC
Mixing Speed:
23r/min
Mixer Motor-Gear Box Power:
2×37kW
Weight:
11500kg
Dimensions:
5650×2480×3280mm
Water distributor
Pneumatic or Hydraulic discharge door
Auto lubrication system
Water distributor
Safety discharge system
Adopts advanced spiral mixing system , which has high efficiency , scale board and mixing blades adopts high-rigidity and high tenacity wearable case alloy steel, to prolong the working life.Centralized oil lubricating system, this system is equipped with overvoltage warning and low oil level warning, safe and reliable.
2. AGGREGATE SYSTEM
2.1 Aggregate batcher:
PLD3200
Volume:
3×15m3
Capacity:
195m3/h
Power:
11kW
Discharge valves:
6unit
Weight:
10200 kg
Dimension:
121200×3920×4800mm
2.2 Weighting hopper:
3units
Load cells:
2000kg(9Unit)
Hopper Capacity:
1.6m3
Power Of Motor:
3kW
2.3 Horizontal belt conveyor:
1 Unit
Dimensions:
1000×31000mm
Conveyor Belt:
δ10mm
Motor:
11 kW
Speed:
1.6m/s
2.4 Mixer feeding belt conveyor
Dimensions:
1Unit, 1000×86000mm
Conveyor Belt:
1Unit , δ10mm
Motor:
37kW
Cover plates:
1Unit
Side Check platform:
1Unit
Speed:
1.6m/s
Feeding belt conveyor is equip with the cover and repair platform ,it can be easy to workout the problem if some thing wrong with it and the emergence stop button can protect the belt conveyor if power off suddenly .
2.5 Aggregate Collecting Bunker
Capacity:
2.5m3
Pneumatic Valve:
Φ300 mm
Vibrate Motor:
3kW
Aggregate Collecting Bunker provide a waiting time for the concrete mixer, it can make sure a enough continues aggregate for the mixer.
3. CEMENT SYSTEM3.1 Cement silo:
4units
Capacity:
100t×4=400t
Silo Diameter:
Φ3000
Plate Thickness:
4~7mm
Silo Pressure Valve:
1unit
Level Indicators:
1unit
Silo Top Filter:
24m2
Ladder, manhole, platform, and parapets are included.
3.2 Cement Screw Conveyor:
4units
Diameter:
Φ273mm
Length:
8m
Capacity
75 ton/hour
Motor Power:
15kW
These silos assure the admixture supply, measuring the amounts by weight, cubic capacity, or load.
4. ADDITIVE SYSTEM
Additive Silo Capacity:
2m3
Load cells:
40kg (1Unit)
Pneumatic Valve:
Φ50mm
Pump:
3kw
Precision:
±1%
5. WATER WEIGNING SYSTEM
Water Weighing Hopper:
1unit
Load cells:
1000 kg (3Units)
Weighting Capacity:
500kg
Motor Power:
3kw
Butterfly Valve:
Φ150 mm
Precision:
±1%
Piping installation on the plant
6. CEMENT WEIGHING SYSTEM
Cement Weighing Hopper:
1unit
Load cells:
500 kg (3Units)
Weighting Capacity:
600kg
Butterfly Valve:
Φ300mm
Precision:
±1%
7. PNEUMATIC SYSTEM
Air Compressor:
1unit
Power:
11kW
Pressure:
1.1MPA
Air flew:
1.2m3/min
Pipe and fittings materials
8. CONTROL SYSTEM
Control Panel with PLC
1unit
Computer display:
17inch
Control Cabin:
1unit
Printer:
1unit
Software:
1unit
All command and control operations, all kind of reporting, failure indications and etc are done by PC Monitor and animation support with PC, printer, UPS and software. Desired amount of receipt can be prepared, customer and truck information can be entered and production information of at least past-one year can be shown.
9. OPTIONAL ACCESSORIES
- Sicoma or BHS concrete mixer.
- Four Bins Bolted Hoppers in place of Batching Bunker.
- Additive System
- Cement & Fly Ash Silo with Screw Conveyor/ Pneumatically Pipe Feeding System.
- Air-condition Control Cabin
- Heating system
- Other special request
PRODUCT TYPE LIST
Search
NEWS
Online Service